5 Factors Impacting Bundled Cable Costs
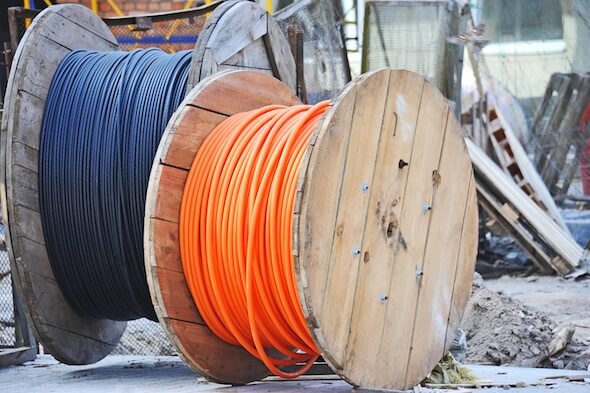
Whenever we speak with electrical contractors and electricians about bundled cable, we are immediately asked “how much does it cost?” and “what are the overall cost savings for my project?”
The answer to these questions are not as simple as one may think since each project has its own set of individual requirements, and our solutions are customized to meet them. There are multiple factors that figure into the final quote price.
Whether pulling singles or pulling a bundled cable through a conduit on an install, the same core costs impact the quote:
- Wire costs
- Labor costs
- Delivery and freight costs
- Overhead costs
- Setup and cleanup costs
1. Wire Costs
First, and foremost, is the cost of the wire itself. If a project requires 100,000 ft of wire, then the cost of the project will reflect the price of the wire. If the wire only contains a small amount of copper, it is less expensive than wire that contains a significant portion. In most cases the larger AWG sized wire represents the largest cost on a project for both the electrical contractor and the manufacturer.
2. Labor Costs
Manufacturing bundled cable requires hands on work in the form of labor. This can be a significant portion of the job costs, which depends on the size of the wire, the amount of connection to terminate, and other variable factors. If a customer needs the wire quickly and the OEM bundled cable manufacturer must have a shift team work overtime, then the OEM’s additional labor costs will be factored into the final price.
3. Delivery and Freight Costs
There is also the freight and 3PL costs for delivering the bundled cable to the job site. Some factors weighed are how quickly the electrical contractor needs the wire and also where in the country it is being delivered.
If electrical contractors need their bundled cable delivery quick, they can either add more labor costs in the form of more electricians on site to expedite the work per shift, or pay a manufacturer to make it and deliver it to the job site by a certain time frame. From a factory perspective, delivery, whether LTL, full truckload, or self- delivery all have an identifiable cost associated with each job being shipped.
For the manufacturer, these can be expensive and run from as low of percentage of the cost as 5% to 6% to as high as 60%. Factors such as distance, size, weight, and minimal charges can influence the cost of delivery. Whereas the contractor may not necessarily think of the hours on the road, hourly wages, tolls, and wear and tear or rental costs to pick up material, the manufacture must include these costs.
4. Overhead Costs
The fourth factor is overhead costs which range from the costs of job trailers, to office space, shop space, to permitting/approvals.
From having all the right local, state, county permits, the correct job safety gear in place, the filing fees, engineering (etc…), some jobs can be a regulatory minefield that are expensive to get through, and more expensive if one attempt to cut corners. The known and stable costs of the business are factored into the hourly rate the contractor charges their customers. From a factory perspective, these costs are also stable and are spread out not in “job hours” but in “factory hours.” From the costs to maintain a UL approval license to rental of fork trucks, many of the costs for the manufacturer are the same month to month. The only variable costs not already covered are those of the reels, binder, tape, and other materials used to make the Quik-Pull bundled cable products.
Many of these are costs electrical contractors pay that are overlooked because they come built in to the products they are already buying.
5. Setup and Cleanup Costs
The fifth cost associated with a job is set up and clean up. From the manufacturer’s standpoint, this is not as significant as it is to the contractor. For instance, at the factory when the job is done there is a little cellophane to recycle, maybe an empty reel or two to recycle, or a fiber board barrel to recycle (usually filled with wire scraps to be recycled).
But from the electrical contractor’s perspective, set up and clean up costs are significant. When it comes to setting up multiple reels, it can take time. With bundled cable, the bundled conductors are on a single reel but it still take time (and hence money) to get the reels from the truck to the right position on the job site. However, bundled cable on a single reel eliminates all of the man hours required for unloading multiple reels of material.
The multiple barrels or reels the factory recycles are a disposal cost for the contractor. The small bits of wire here and there are thrown in the dumpster and add pounds to the overall tonnage and thereby the costs, the packing and warehousing of left over useable wire also drive up labor costs for the electrical contractor since he or she now need to devote labor time to cleaning up the job site.
Looking at the Whole Picture
To summarize, the total costs of bundled cable and its final cost-savings for an electrical contractor include number of variables. Each quote is unique and will vary based on the factors listed above.
To learn more about the cost-saving value of bundled cable, check out our price comparison page.
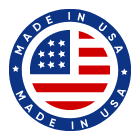
READY TO SAVE TIME & MONEY WITH BUNDLED CABLE?
Get a quote on our custom cable bundles today.